About Friction Welding
Features of friction welding
- Save material costs and reducing process time
- High durability because the whole surface of the joint is bonded at the atomic level
- Because different materials can be bonded, costs are reduced while still retaining functionality
- Even seemingly impossible combinations, such as copper and aluminum, can be achieved with very high durability
- Friction welding does not need a soldering iron or solvent, and has low CO2 emissions, so it has little impact on the environment
- Automatic processing with friction welding machines does not require dexterity and has high repeatability
Make it possible with friction welding
Case : from material φ150×350L cut to φ145×45L + φ75×300L…
Friction-welding case
150×50L material and 80×300L material are joined and cut.
Can save material costs accordingly.
Costs can be reduced by using only high-quality materials for the necessary parts and friction welding for other low-priced materials.
Minimal material and cost savings
Easily lighten the weight of commercially available tubes by capping both tube ends using friction welding.
Possible to reduce weight easily
Durability test
Friction welded products have the same tensile strength as the parent materials, whether combining the same or different materials. The joints are not peeling off even under torsional strength and bending tests.
Tensile testing
Use tensile testing machine to test SUS304 + A1050 friction welded products.
Fractures around the weld.
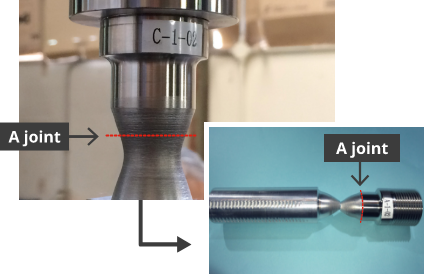
Torsional strength test
Use torsion machine to test S35C+S35C friction welded products.
Fractures around the weld.
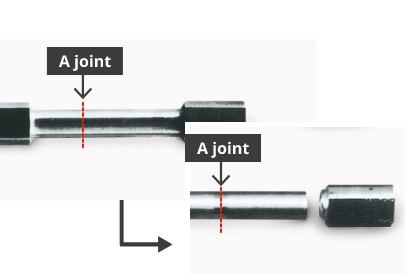
Bending test
Test the shape of SUS304+A1070 friction welded tube by cutting it into strips and bending them inward and outward.
No breakage at the joint.
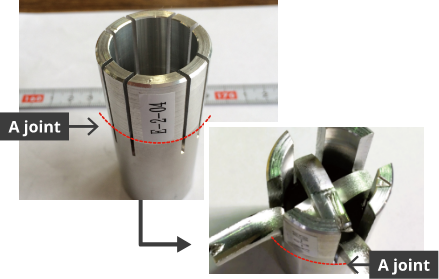