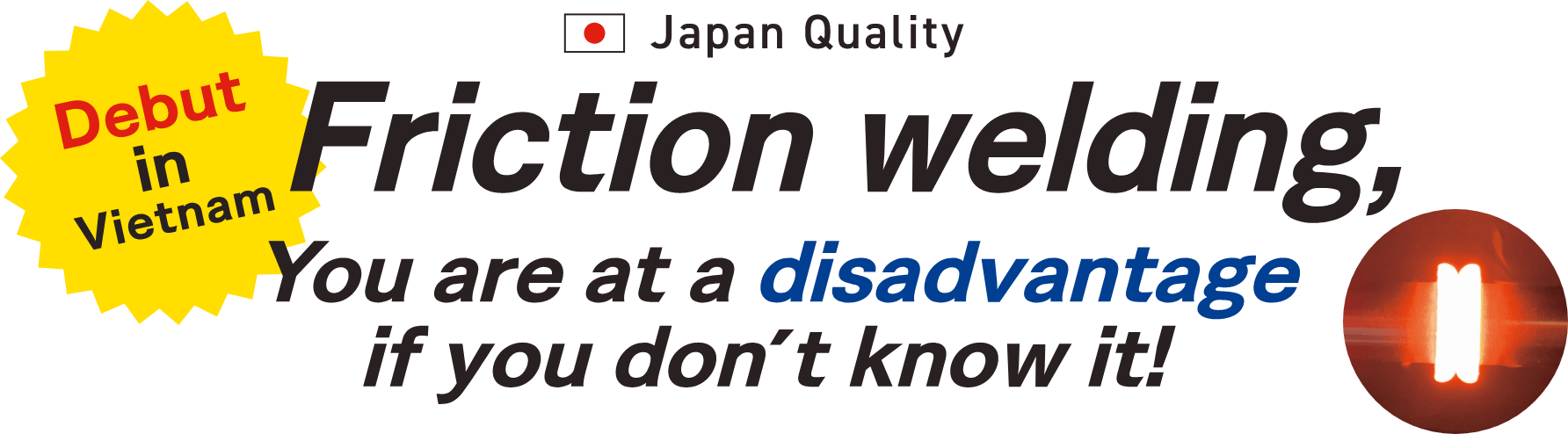
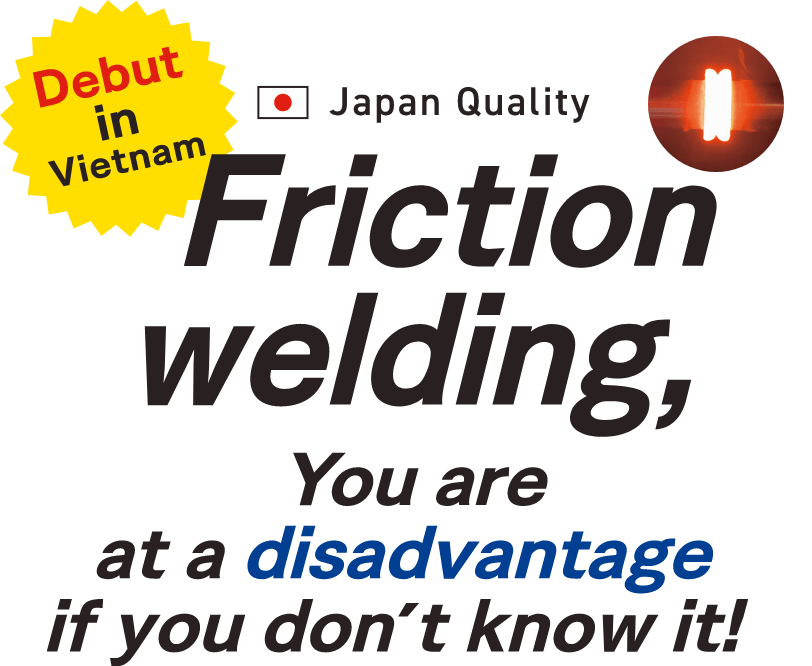
YORISHIRO’s friction-joining technology
simultaneously reduces costs from materials to processing, and shortens delivery times.
-
Case : from material φ150×350L cut to φ145×45L + φ75×300L…
Friction-welding case150×50L material and 80×300L material are joined and cut.
Can save material costs accordingly.
-
Costs can be reduced by using only high-quality materials for the necessary parts and friction welding for other low-priced materials.
Minimal material and cost savings!
-
- Processing time is long, and costs such as processing costs and cutlery costs are high.
- Caught up in price competition have no profit.
-
- Time-consuming and costly for metal mold making.
- Mold maintenance is difficult.
- Lower-quantity orders are difficult.
-
- Before welding, it is necessary to do machining.
- There are variations in the finish depending on the worker.
- Having trouble with export standards.
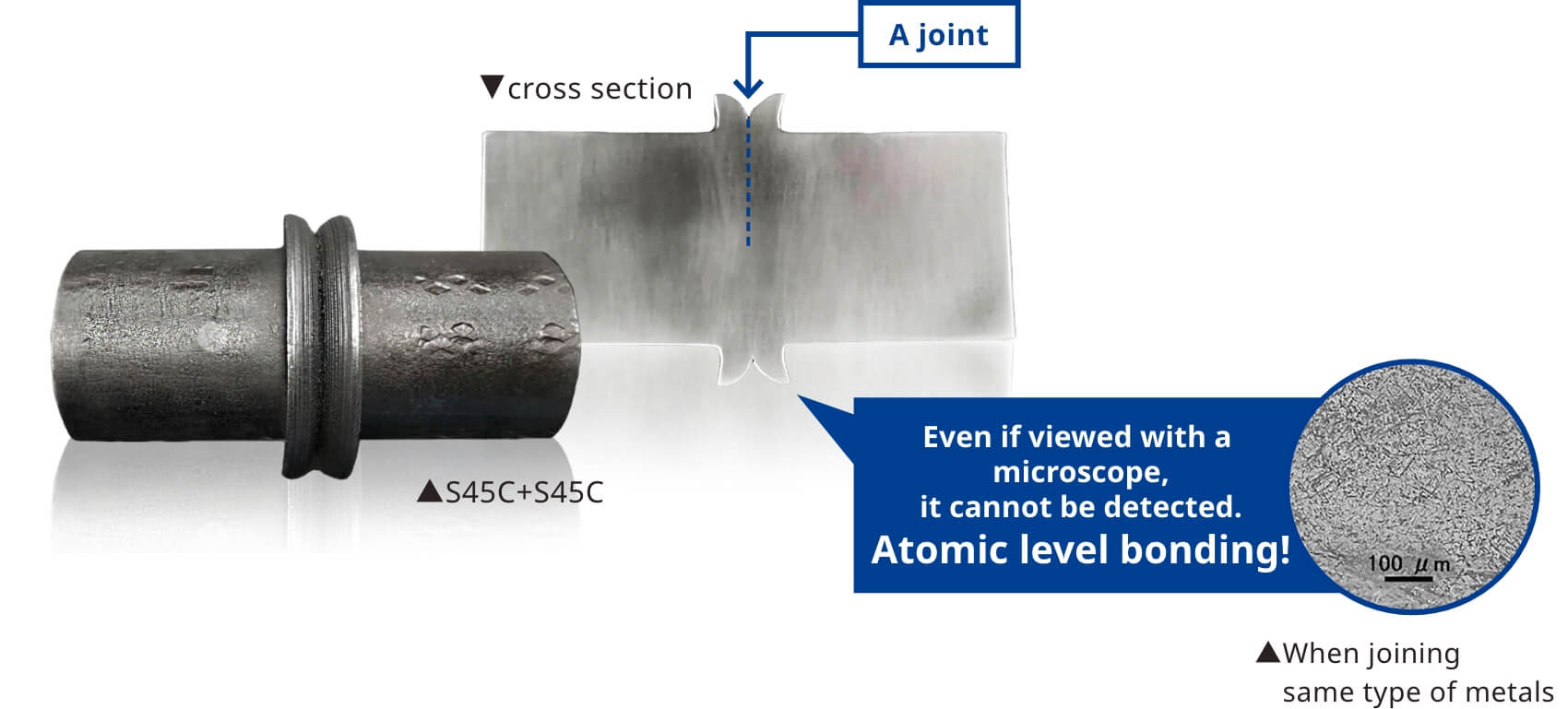
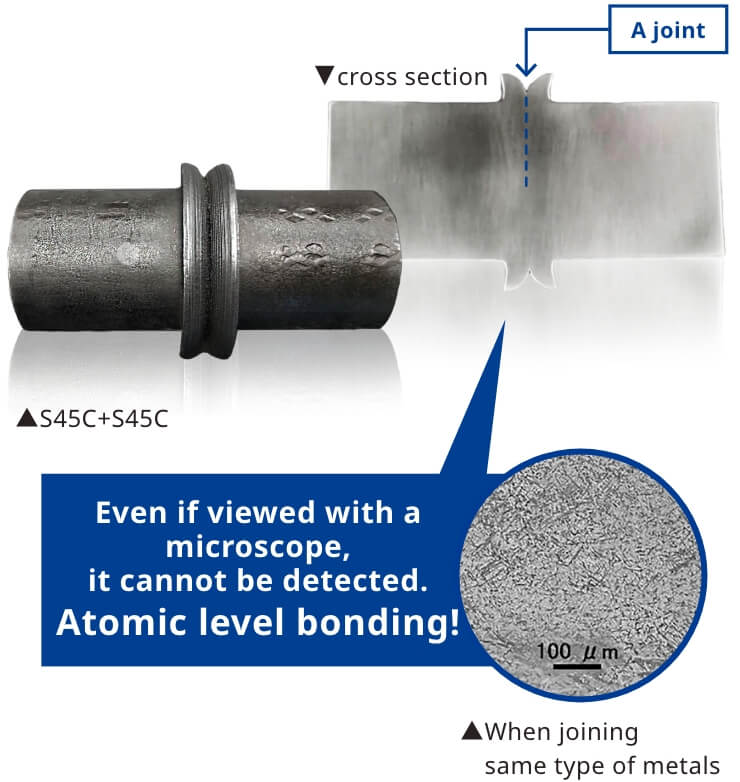
Features of friction welding
- Save material costs and minimize working hours.
- High durability because the whole surface of the joint is bonded at the atomic level.
- Because different materials can be bonded, costs are reduced while still retaining functionality.
- Even seemingly impossible combinations, such as copper and aluminum, can be achieved with very high durability.
- Friction welding does not need a soldering iron or solvent, and has low CO2 emissions, so it has little impact on the environment.
- Automatic processing with friction welding machines does not require dexterity and has high repeatability..
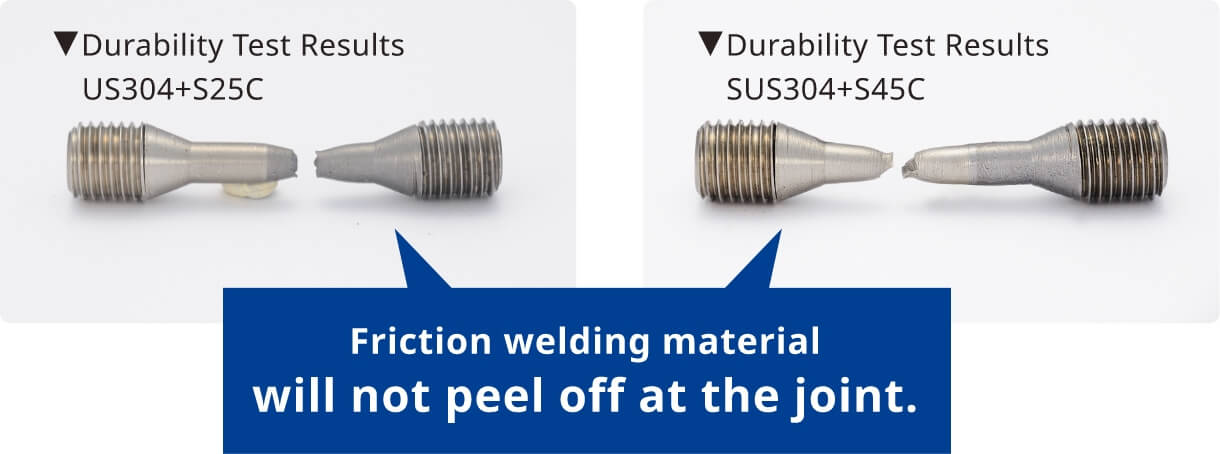

Example of product
Proceed to cutting from friction-welded materials.
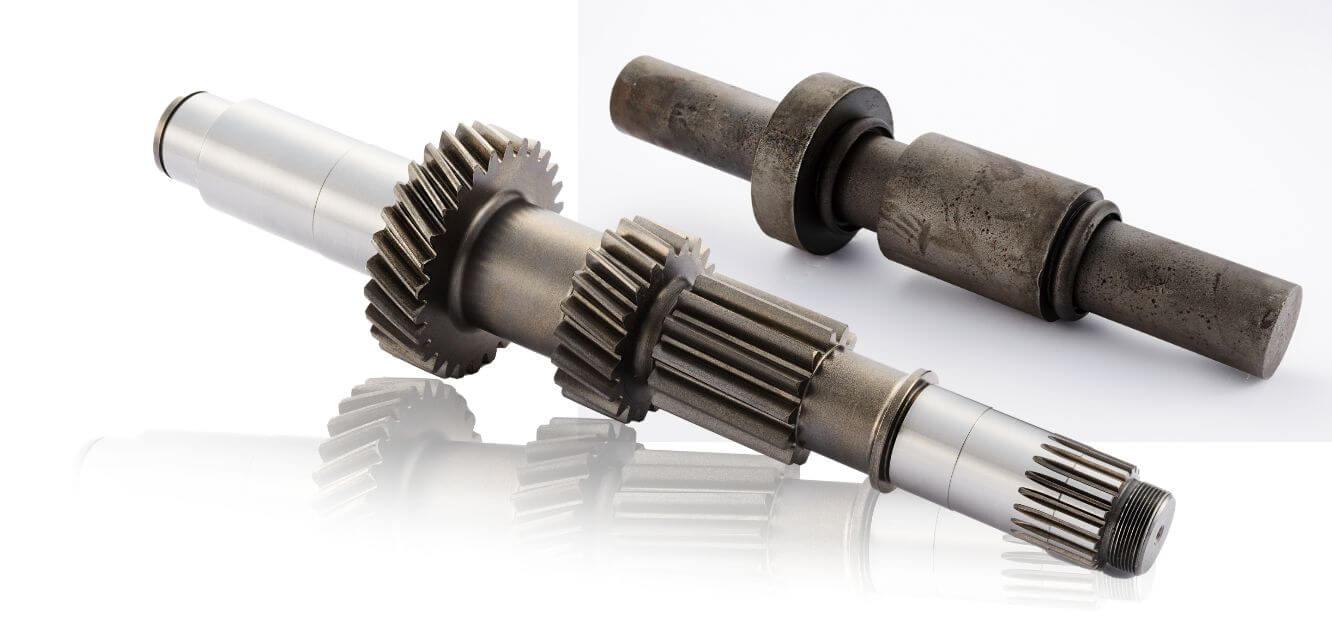
SCM435+SCM435+SCM435
friction welding
-
Marine pump shaft
S25C+SUS304 -
A screw shaft
SUS304+SUS304+SUS304 -
Low-temperature pipe
SUS304+A1050 -
Power terminals A1050+C1020
Friction welding products/after processing・plating -
Using copper and aluminum to make Japanese-style drinking cups